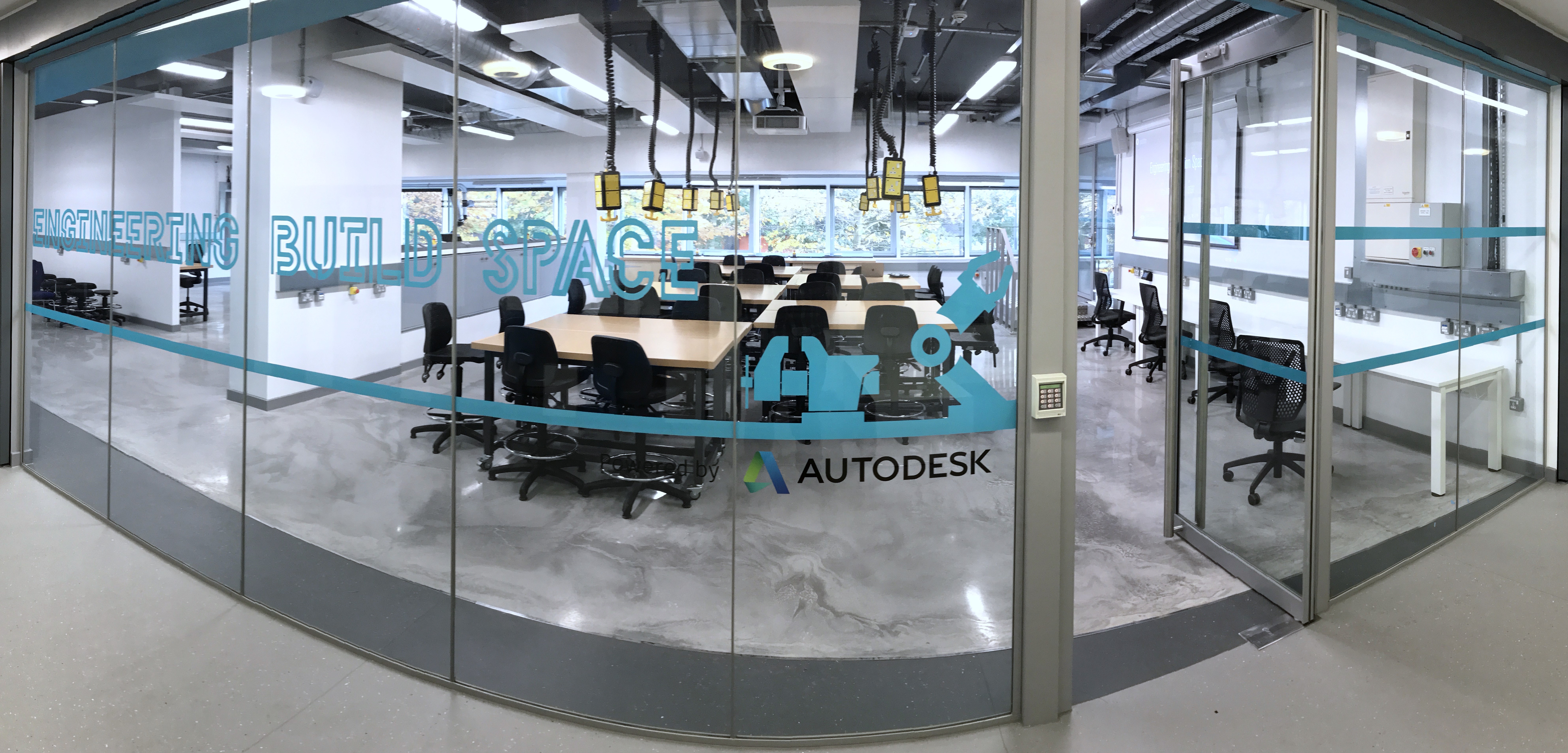
Hi!
Welcome to the Engineering Build Space! The EBS is a makerspace situated in the School of Engineering at the University of Warwick where all students and staff have access to equipment, facilities and expertise to help realise their designs.
For more general information about the space, please see our About page.
You're currently not signed in, so will have limited access to the functions and information here.
If you a student or memebr of staff at Warwick, please Sign in